NDT II, III
Certified Welding Inspections and Integral Testing Solutions
Certified Welding Inspection
Making sure your assets have the Seamless Quality you look for.
​Seamless Quality Solutions can carry out your certified weld inspections according to the requirements established by the American Welding Society (AWS), the American Petroleum institute (API), or any other internationally accepted welding codes accepted by the applicable industries, including regulations for structural steel, building, pipelines, and bridge construction.




Non-Destructive Testing
(NDT, NDE, NDI)
For large, expensive components and structures, which may be assembled and joined at their final location, it is not practical, and is often impossible, to assure quality by destructively testing a statistical sampling of the product. There may be only one bridge, one nuclear containment vessel being built, and that one must be certified to meet all regulations that apply. Even in applications involving multiple builds of the same design, such as in ships or aerospace applications, weld joints requiring inspection may be inaccessible to direct visual inspection. Non-destructive testing is the answer in these situations.
The methods selected depend on the physical properties of the materials to be inspected, their geometry, their accessibility, and any legal requirements governing quality control for safety-critical systems.

Magnetic Particle Inspection
Magnetic Particle Inspection is a way to provide qualitative visual enhancement of near-surface cracks and defects. In brief, an appropriate magnetic field is applied to the weld or part to be inspected, and then magnetic particles, either dry or suspended in a suitable liquid, are applied to the surface. Wherever the magnetic flux lines are interrupted by a defect, the magnetic particles will gather and highlight the crack or void.
​
This method is attractive due to its low cost, its ability to be able to be used on virtually any shape of component and the moderate skill level required to conduct the testing with useful results.
However, Magnetic Particle Inspection is not appropriate for every application. It only works on ferromagnetic materials, it is limited to detection of superficial and thin-section defects, the orientation of the defects and the correct application of the magnetic field requires expertise, and some components must be demagnetized after use.
Ultrasonic Shear Wave Inspection
Shear wave, or angle beam ultrasonic inspection is a technique that detects discontinuities in dense crystalline materials by detecting reflected ultrasonic waves transmitted through a material. The discontinuities can be cracks or unjointed segments of welds, pores, or any other defect that results in a void where solid material is expected.
This method is best applied to metals, but works, with less resolution in detecting size and location, in other materials such as ceramics, concrete and plastics. Ultrasonic inspection is a highly effective method for inspecting large and visually inaccessible joints and members. It is particularly valuable in leaving the inspected material completely unchanged, with no residue or damage of any kind.
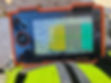
Liquid Penetrant Inspection (LPI)
Liquid Penetrant Inspection is appropriate for the qualitative detection of defects that reach the surface of the joint or material to be inspected. It is a simple and low-cost method of detecting hairline cracks, surface porosity and fatigue damage in a wide range of materials. A liquid dye, whether fluorescent or of a color with appropriate contrast to the material being inspected, is wiped across the part. Capillary action draws it into any tiny crevices. The component is then visually inspected for evidence of dye remaining where it is not expected.
It is relatively inexpensive and requires a lower operator skill level than some other inspection techniques, but this method can only be applied to non-porous materials with a relatively smooth surface. Any potential difficulties in pre-cleaning the surface beforehand or in completely removing the dye afterward must be considerations.
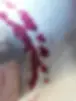
Mechanical Testing
Mechanical tests are important when developing the base materials for any application. In heavy or safety-critical welded structures, certification of welding processes using test samples that include the weld itself is often required. These tests maybe be performed under a variety of standard procedures, including ANSI, AWS and ASTM specifications. Tensile, Hardness and Bend tests are all test methods that Seamless Quality can perform for you under controlled conditions.
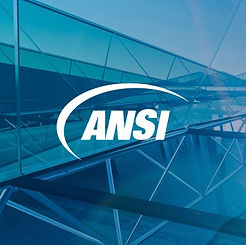
Tensile Testing
Testing of samples containing actual welds can require special builds or machining of test samples from actual parts. A controlled sample shape and size is tested by applying steadily increasing load until the sample breaks. The resulting load vs elongation data, combined with the geometry of the sample, yields standardized information on the strength, ductility and toughness of a weld procedure. For example, a welding procedure that produces unintended brittle phases in steels will reveal the problem as a lack of elongation before breaking. NDT Jax can design weld samples and test procedures that comply with standards and regulations and provide the certification information you need.
Hardness Testing
Hardness testing (Brinell, Rockwell, Vickers) is mostly useful for evaluating new units, but can also be used in the field to inspect for changes due to the service environment such as operation in hot or corrosive environments. Hardness is broadly correlated with strength, so it gives a quick, non-destructive indication of whether the part or structure has been properly welded, heat-treated or case-hardened, or whether the material has changed in hardness, and thus, expected strength and fatigue resistance, in service. A new weld that does not yield the expected hardness indicates a serious issue that must be addressed.
Bend Testing
Bend testing in the context of welding (usually butt welding) consists of joining two pieces of production-intent material using a production-intent procedure, and then forcing the test piece, with the weld at the centerline, into a standardized U-shaped fixture under controlled test conditions. This test is used as part of certifying a weld’s ductility and strength in bending. If failure or incipient failure is observed during this test, the weld procedure and components that use that procedure cannot be certified.
Proof Testing
Proof testing is a direct method of testing new or existing components, structures, rigging and pressure vessels to show that they are strong enough to survive an overload that exceeds the maximum allowable working load, but is less than the yield strength of the tested system, i.e. less than the applied load at which plastic deformation will begin. Although this method does not alert the tester to small defects which may become important at a later date due to fatigue, corrosion, erosion or other service life hazards, it does show that a structure is capable of performing its intended function at the time it was tested, and that it meets Occupational Safety and Health Administration (OSHA) standards. ​